Legierungen mit „Gedächtnis“, Materialverbunde mit integrierten Funktionen oder Textilien, die Beton stabiler und haltbarer machen als Stahl – das sind einige der Werkstoffe, aus denen die Zukunft gemacht wird. Erdacht und in Produkte verwandelt werden sie in der Region Dresden. Hier konzentriert sich Deutschlands Forschung zum Leichtbau mit Anwendungspotenzial nicht nur für den Fahrzeugbau. Zur 2. Werkstoffwoche Ende September 2017 konnte die Elbmetropole erneut als deutsche Leichtbau-Hauptstadt überzeugen.
Wie bereits zur Premiere 2015 nutzten mehr als 1800 Werkstoffexperten aus dem In- und Ausland die Tage vom 27. bis 29. September 2017, um sich über neueste Entwicklungen auf dem Materialsektor zu informieren und auszutauschen. „Werkstoffe entscheiden über erfolgreiche Produkte und Industrien. Dresden ist ein exzellenter Leuchtturm in Deutschland für diesen Bereich. Deshalb sind wir hier“, betonte Dr. Frank O. R. Fischer, geschäftsführendes Vorstandsmitglied der Deutschen Gesellschaft für Materialkunde (DGM), einem der Veranstalter der Werkstoffwoche, und sagte weiter: „Wir müssen mehr Mut zu neuen Ideen haben und stärker in diese investieren. Weltweit steht Deutschland für erstklassige Ingenieursleistung. Den Vorsprung, den sich der Industriestandort Deutschland im Laufe der vergangenen Jahrzehnte erarbeitet hat, muss er behalten und darf ihn jetzt nicht an aufstrebende Länder aus Asien abtreten. Neue Werkstoffe haben enormes Potenzial, Deutschlands Industrie als Innovator und Trendsetter zu stärken. Wer heute in die Weiterentwicklung und die Anwendung neuer Materialien investiert, verschafft sich einen erheblichen Wettbewerbsvorsprung.“ Entwickler und Anwender zusammenbringen und gemeinsam Innovationen vorantreiben, dafür sei die Werkstoffwoche die richtige Plattform, ergänzte Dr. Peter Dahlmann, geschäftsführender Vorstand des Deutschen Stahlinstituts VDEh, ebenfalls Veranstalter der Werkstoffwoche.
Kühne Idee: Produzieren direkt im All
Eine kühne Idee stellte der Materialwissenschaftler und ESA-Astronaut Dr. Matthias Maurer vor, der Werkstoffe als Schlüssel für eine erfolgreiche Raumfahrt bezeichnete. Gepaart mit neuen Fertigungsverfahren wie Additive Manufacturing wird es möglich, die derzeit in Entwicklung befindliche Rakete Ariane 6 um 30 Prozent günstiger herzustellen als ihre Vorgängerin. In Zukunft sollte es dank additiver Verfahren gelingen, Weltraum-Equipment wie Satelliten direkt im All zu bauen. Damit würde der Aufwand auf der Erde für die Produktion höchstbelastungsgerechter Antriebe, die für eine nur wenige Minuten dauernde Startphase ausgelegt sind, deutlich reduziert.
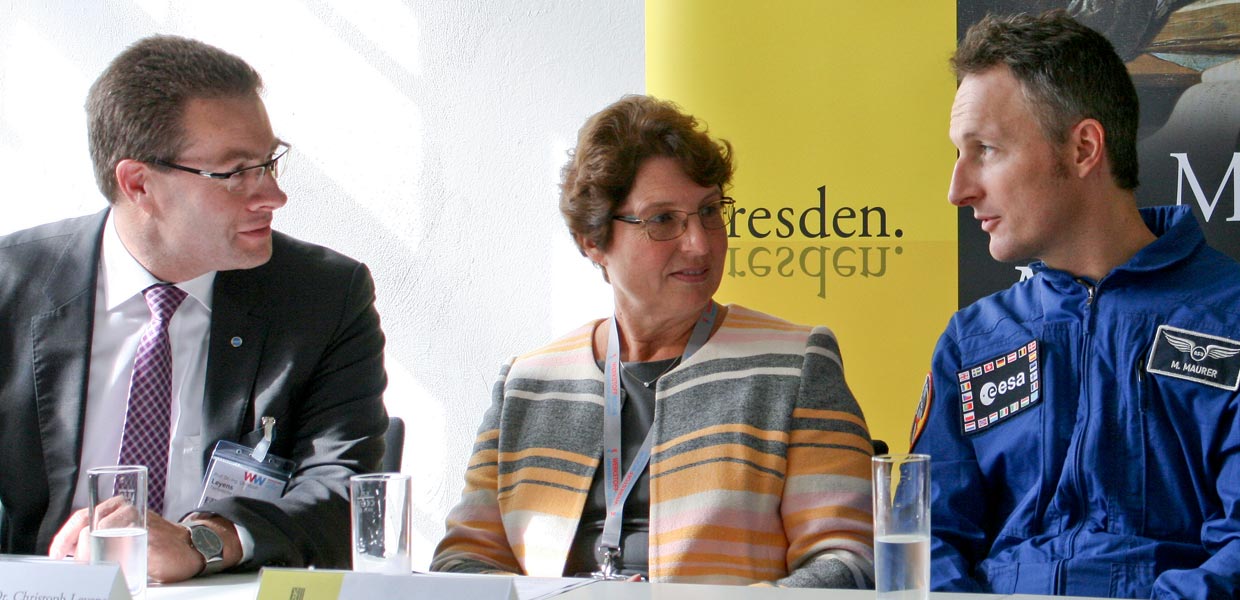
Materialwissenschaftler und ESA-Astronaut Dr. Matthias Maurer (r.) sprach über die Vision, zukünftig direkt im All zu produzieren, auf dem Foto im Gespräch mit Prof. Brigitte Voit, Vorstandsvorsitzende des Materialforschungsverbundes Dresden und Direktorin des Leibniz-IPF, und Prof. Christoph Leyens, Mitglied der Institutsleitung des Fraunhofer IWS. (Foto: Ina Reichel)
Größte europäische Forschungsallianz für 3D-Druck
Was Additive Manufacturing vermag, war ein Hauptthema in den Sessions der Werkstoffwoche. Was es bereits heute leistet, ist am Fraunhofer IWS in Dresden zu sehen. Das von diesem Institut geleitete Konsortium AGENT-3D hat mit über 120 Partnern aus Forschung und Industrie ein strategisches Bündnis im Bereich der additiv-generativen Fertigung aufgebaut, um Deutschland den Vorsprung in diesem Bereich zu sichern. „Mit AGENT-3D verfügt Deutschland über eine schlagkräftige Forschungsallianz für Additive Fertigung, die größte in Europa. Unser gemeinsames Ziel ist es, diese innovative Technologie zur Schlüsseltechnologie für die Industrie 4.0 zu entwickeln“, sagt Prof. Christoph Leyens, der das Forschungscluster des gleichnamigen Projektes „AGENT-3D: Additiv-Generative Fertigung – Die 3D-Revolution zur Produktherstellung im Digitalzeitalter“ koordiniert und zudem Mitglied der Institutsleitung des Fraunhofer-Instituts für Werkstoff- und Strahltechnik IWS und Direktor des Instituts für Werkstoffwissenschaft der TU Dresden ist. Zu den Clusterpartnern zählen die Siemens AG und Rolls Royce Deutschland. Das Verbundvorhaben wird vom BMBF im Rahmen seines Programms „Zwanzig20 – Partnerschaft für Innovation“ mit rund 45 Millionen Euro gefördert; die Industriepartner beteiligen sich mit einem finanziellen Beitrag in ähnlicher Größenordnung.
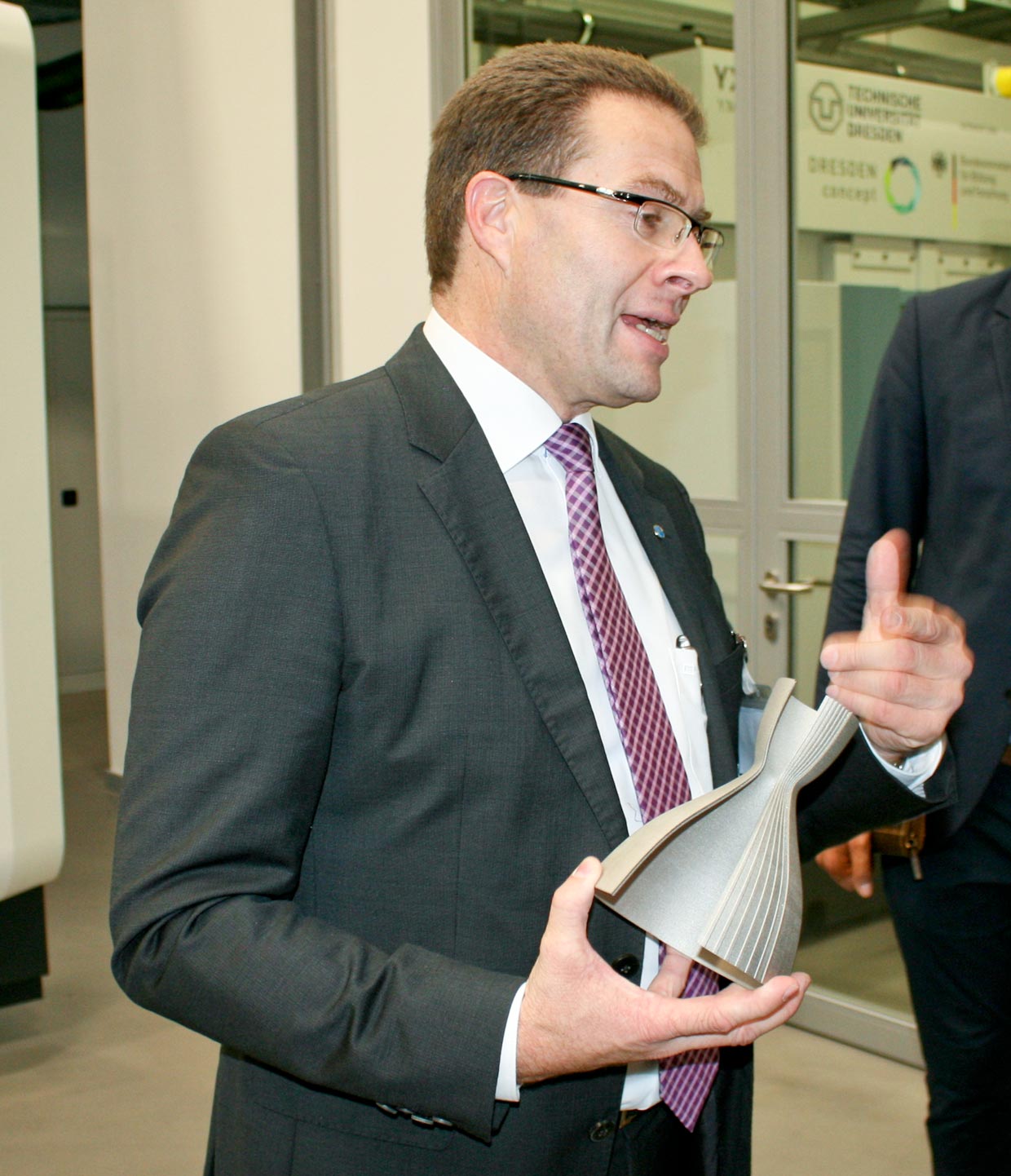
Prof. Christoph Leyens stellt eine additiv gefertigte Brennkammer mit integrierten Kühlkanälen für eine Raumfahrtanwendung vor. Während das Modell aus Stahl ist, werden die Originalteile aus teurem Titan effizient gefertigt. (Foto: Ina Reichel)
Geballte Fraunhofer-Werkstoffkompetenz in Dresden
Neben dem IWS arbeiten in Dresden weitere Fraunhofer-Institute an den Werkstoffen von morgen. Das Fraunhofer IKTS deckt das Feld der Technischen Keramik von der grundlagenorientierten Vorlaufforschung bis zur Anwendung in seiner ganzen Breite ab und qualifiziert keramische Technologien und Komponenten für neue Branchen, neue Produktideen und neue Märkte. Ein Beispiel dafür ist transparente Keramik, die Fahrzeugscheiben vor Munition aus Schusswaffen schützt.
Der Institutsteil Dresden des Fraunhofer IFAM ist spezialisiert auf Verbund- und Gradientwerkstoffe, Funktionswerkstoffe und hochporöse metallische Werkstoffe. Die innovativen Lösungen finden vor allem Anwendung in den Bereichen Fahrzeugbau, Elektronik, Maschinenbau, Raumfahrt, Energietechnik und Medizintechnik.
Das Fraunhofer FEP ist ein führender Forschungs- und Entwicklungspartner für Oberflächentechnologien und organische Elektronik. Organische Halbleiter ermöglichen großflächige Bauelemente wie organische Leuchtdioden (OLED) oder organische Solarzellen auf flexiblen Trägermaterialien. Das FEP verfügt über Kompetenz entlang der gesamten Wertschöpfungskette für flexible OLED-Module – vom blanken Substrat bis hin zu einer integrierten Leuchte.
Carbonbeton – Baustoff der Zukunft
Ein Baustoff mit enormem Zukunftspotenzial ist ebenfalls „made in Dresden“ – Carbonbeton. Wie sehr die Baubranche neue Ideen braucht, zeigt das C3-Projekt von Prof. Manfred Curbach und seinem Team: „Seit Jahren kämpfen wir gegen den schlechten Ruf des Betons. Beton ist nach Wasser das am meisten verwendete Material. Jährlich werden weltweit acht Milliarden Kubikmeter Beton verbaut. Um diese Zahl greifbar zu machen, muss man sich einen gewöhnlichen Tennisplatz vorstellen, um den wir einen Turm mit einer Wandstärke von 30 Zentimeter bauen. Dieser Turm hätte eine Höhe von etwa 384.000 Kilometer und würde bis zum Mond reichen. Mit Carbonbeton revolutionieren wir nicht nur die Baubranche, sondern schonen ebenfalls die wertvolle Umwelt. Der Ersatz des korrosionsanfälligen Stahls durch Carbon bietet eine kostengünstige, flexible und bis zu 80 Prozent materialreduzierte Alternative, da eine zusätzliche Betondeckung zum Schutz vor Korrosion nicht mehr notwendig ist“, so Prof. Manfred Curbach, C3-Vorstandsvorsitzender und Direktor des Instituts für Massivbau der TU Dresden. 2016 haben die TU Dresden-Professoren Manfred Curbach, Chokri Cherif, Peter Offermann und ihr Projekt „Das faszinierende Material Carbonbeton – sparsam, schonend, schön“ den Deutschen Zukunftspreis erhalten. Parallel zur Werkstoffwoche fanden in Dresden vom 26. bis zum 27. September die Carbon- und Textilbetontage 2017 statt. Bei dieser Expertentagung mit rund 350 Teilnehmern wurden sowohl Forschungsergebnisse aus dem C3-Projekt als auch praktische Anwendungsbeispiele von Carbon- und Textilbeton präsentiert.
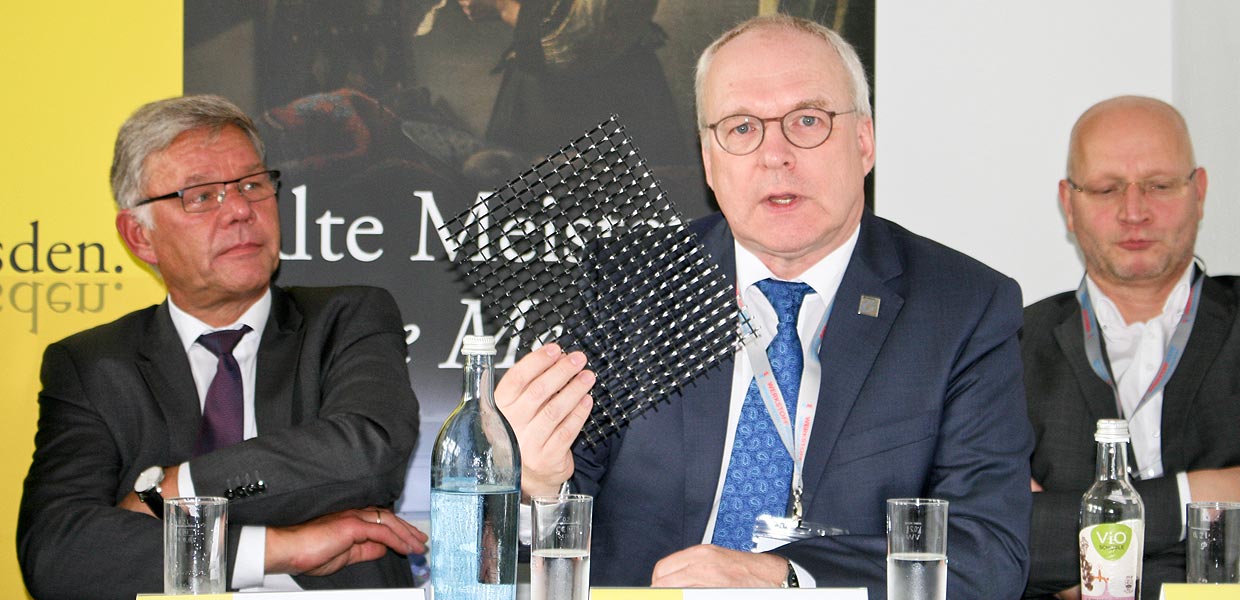
Das Grundgerüst für das neue Baumaterial Carbonbeton sind diese leichten, aber sehr stabilen und nicht korrodierenden Strukturen aus Fasern, die Prof. Manfred Curbach zeigt. (Foto: Ina Reichel)
ILK bildet Entscheider von morgen aus
Initiator und Treiber für den in der Fachwelt als Dresdner Modell bekannten Funktionsintegrativen Systemleichtbau in Multi-Material-Design ist das 1994 von Prof. Werner Hufenbach gegründete Institut für Leichtbau und Kunststofftechnik (ILK) der TU Dresden. Am Rande der Werkstoffwoche stellte ILK-Vorstand Prof. Hubert Jäger einer Fachjournalisten-Delegation das Leistungsspektrum des Instituts vor, das auf einer über 60-jährigen Leichtbau-Erfahrung in Dresden basiert. Aktuell führen rund 240 Mitarbeiter umfangreiche Forschungs- und Entwicklungsarbeiten auf dem Gebiet des ressourcenschonenden Leichtbaus für den Fahrzeug- und Maschinenbau, die Luft- und Raumfahrt, die Energietechnik, Medizintechnik Sportgeräteindustrie, das Bauwesen und weitere Anwendungsindustrien durch. Jährlich erlangen etwa 100 Absolventen den Leichtbau-Master. „Wir bilden die Entscheider von morgen aus und nutzen dafür modernste Technologien. Ein halbjährliches Review bei den Lehrinhalten sichert hier beste Qualität“, betonte Prof. Jäger. Das ILK ist mit den Technischen Universitäten Chemnitz und Freiberg Teil der Leichtbauallianz Sachsen und sichert die starke Position der Region beim hybriden Leichtbau als dem System der Zukunft. Bei alldem dürfe man das in Deutschland erreichte Leichtbau-Know-how nicht aufs Spiel setzen. „In China und Korea werden Milliarden investiert. Diese Regionen haben uns in fünf Jahren überholt, wenn wir so weiter dümpeln und in Deutschland und Europa die Forschungsgelder immer noch mit der Gießkanne verteilen. Wir brauchen eine Entwicklungspolitik, die unsere Stärken stärkt. Wenn wir nicht die Technologieführerschaft halten, ist Deutschland übermorgen ausgeblutet“, schickte er einen eindringlichen Appell in Richtung politischer Entscheider. Das ILK entwickelt eine eigene Internationalisierungsstrategie, die sich vor allem nach China, Südkorea und Singapur orientiert. In diesem Kontext ist die Ende September 2017 erfolgte Gründung des Korea-Germany Materials Center (KGMC) zu sehen. Neben dem ILK sind das Fraunhofer IKTS Dresden und das Korea Institute of Materials Science KIMS Partner in diesem Verbund.
Das ILK bildet als einziges Institut in Europa die komplette Leichtbau-Prozesskette ab und nutzt dafür auch die Verbindung zu Ausgründungen wie der Leichtbau-Zentrum Sachsen GmbH. Mit weiteren Partnern haben Unternehmen und Institut z. B. das serienfähige Ultraleichtbau-Projektfahrzeug InEco auf die Räder gestellt. Das elektrisch angetriebene Kompaktfahrzeug mit CFK-Teilen wiegt weniger als 900 Kilogramm und besteht aus deutlich unter 100 Teilen. Die in der Herstellung teuren Carbonfasern noch maßgeschneiderter in punkto Festigkeit, Steifigkeit und Porosität einzusetzen, z. B. als Energiespeicher, ist eine wesentliche Forschungsaufgabe.
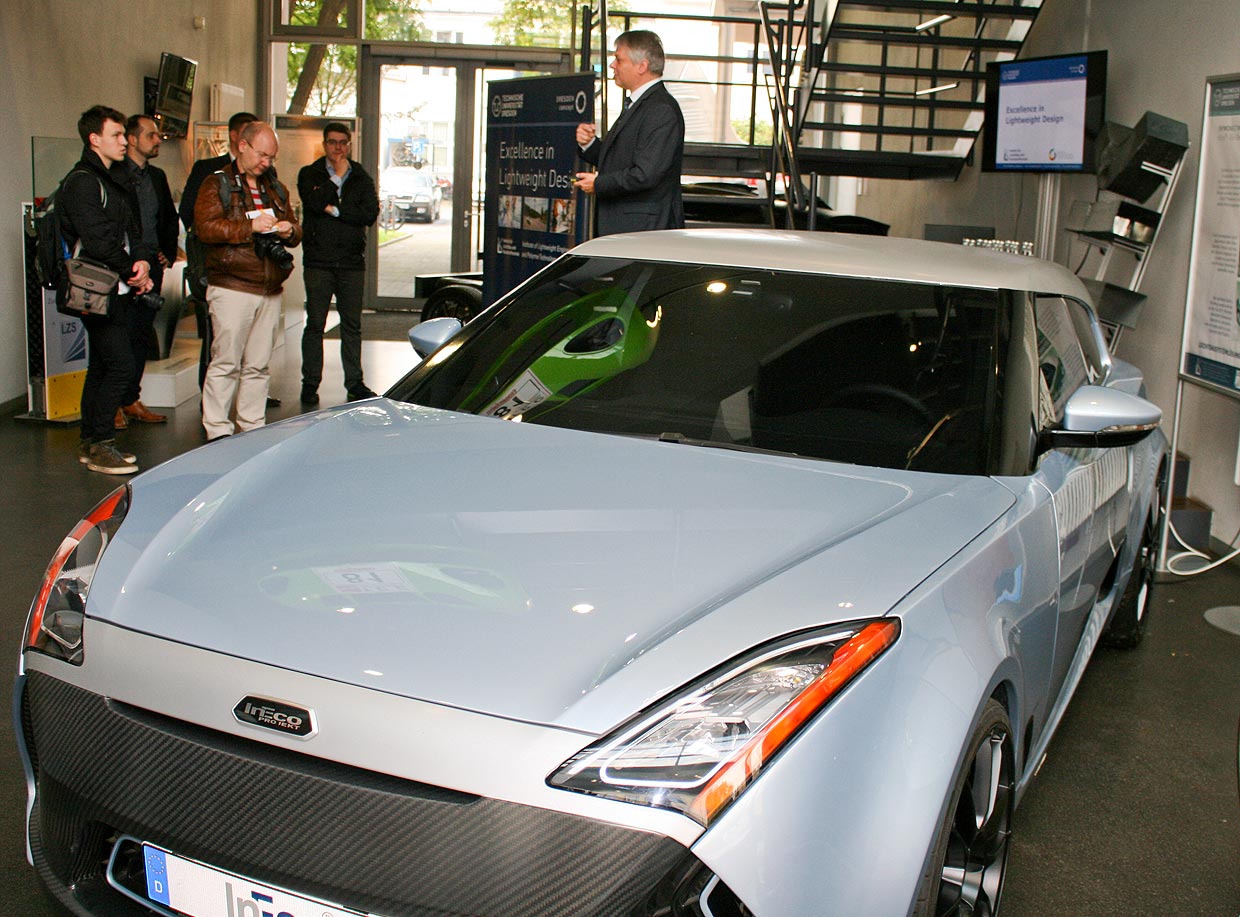
Das Institut für Leichtbau und Kunststofftechnik der TU Dresden bildet als einziges Institut in Europa die komplette Leichtbau-Prozesskette ab und nutzt dafür auch die Verbindung zu Ausgründungen wie der Leichtbau-Zentrum Sachsen GmbH, wie Institutssprecher Prof. Hubert Jäger betonte. Mit weiteren Partnern haben Unternehmen und Institut z. B. das serienfähige Ultraleichtbau-Projektfahrzeug InEco auf die Räder gestellt. (Foto: Ina Reichel)
LSK investiert in „SuperTooler“
Zu finden ist das Know-how des ILK bereits in vielen Industrieanwendungen. Dafür sorgen die Ausgründungen aus dem Institut. So trägt die Frontmaske des neuen ICE 4 mit die „Handschrift“ der Leichtbau-Systemtechnologien KORROPOL GmbH Dresden (LSK), wie Geschäftsführer Sammy Techritz berichtet. Ebenso ist eine neue Generation Luftführungsringe für Großgeneratoren „made by LSK“. Bei den Luftführungsringen realisiert das Unternehmen die komplette Prozesskette und liefert die Produkte exklusiv für Siemens in die USA. Auch für Straßenfahrzeuge, für den Rennsport sowie für Oldtimer entwickelt und fertigt das Unternehmen individuelle Bauteile aus hochbelastbaren Faserverbundwerkstoffen. Die fertigungsgerechte Konstruktion sowie die Herstellung von Formen und Modellen gehört ebenfalls zur LSK-Expertise. Speziell für letztgenannten Bereich investiert das 25-köpfige Unternehmen in eine Hybrid-Produktionszelle, in der sowohl additiv als auch subtraktiv gearbeitet werden kann. Mit diesem „SuperTooler“ sind Großstrukturen bis acht mal zwei mal zwei Meter einfach herstellbar. Die Produktionszeit für Formen und Modelle verkürzt sich um ca. 50 Prozent. Die Kunststoff-Modelle werden werkstofflich recycelbar bzw. aus recycelten Werkstoffen gefertigt und damit in einem geschlossenen Werkstoffkreislauf.
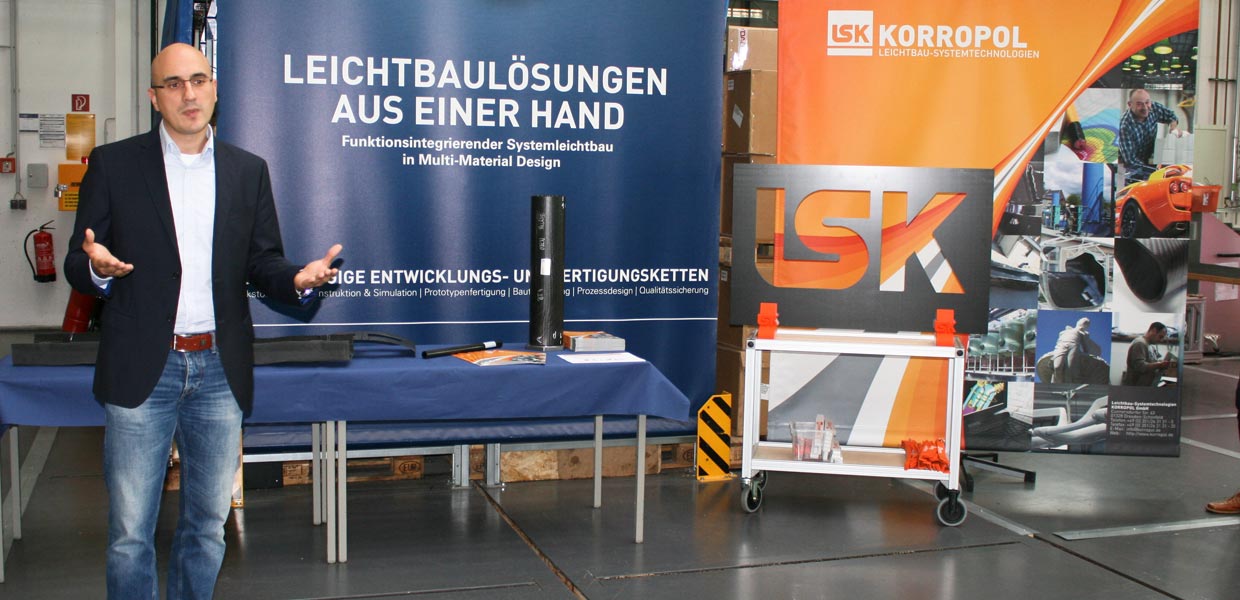
Sammy Techritz, Geschäftsführer der LS KORROPOL GmbH, stellte die Leichtbaukompetenzen des Unternehmens vor und verwies auf die Aktivitäten im Bereich 3D-Druck. So investiert LS KORROPOL in einen „SuperTooler“, mit dem Großstrukturen bis acht mal zwei mal zwei Meter einfach herstellbar sind. Die Produktionszeit für Formen und Modelle verkürzt sich um ca. 50 Prozent. (Foto: Ina Reichel)
Skalierbare Batteriesysteme dank Leichtbau
Den Leichtbau für einen besseren Einsatz der Elektromobilität nutzt die jüngste ILK-Ausgründung SCABA GmbH Dresden. Statt Pouch- oder prismatische Lithium-Ionen-Zellen setzt SCABA – die Abkürzung steht für skalierbare Batteriesysteme – auf die gut verfügbaren Rundzellen. Aus Kunststoffstrukturen und hauchdünnen Blechen entstehen Zellverbinder, mit denen beliebige, geometrieunabhängige Bauräume konturiert werden können. „Aus standardisierten, vorgefertigten Kunststoff-Metall-Verbindern lassen sich spezifische Batterieblöcke ohne den Umweg über Module fertigen“, beschreibt Mitgründer und Gesellschafter Marco Zichner die Idee hinter SCABA. Die Effekte können sich sehen lassen: SCABA-Systeme sind etwa 20 Prozent günstiger als andere verfügbare einbaufertige Systeme und weisen eine um ca. 30 Prozent höhere Energiedichte auf. Marco Zichner sieht einen Markt insbesondere bei Kommunalfahrzeugen, Gabelstaplern, Bussen, weiteren Sonderfahrzeugen sowie Industrieanwendungen. Seit Gründung 2015 wurden bereits 14 Projekte mit 50 Batteriesystemen realisiert. Das Unternehmen strebt eine weitere Industrialisierung an und plant ein eigenes Werk in Dresden. Das ehrgeizige Ziel bis 2022 heißt 100 Millionen Euro Umsatz.
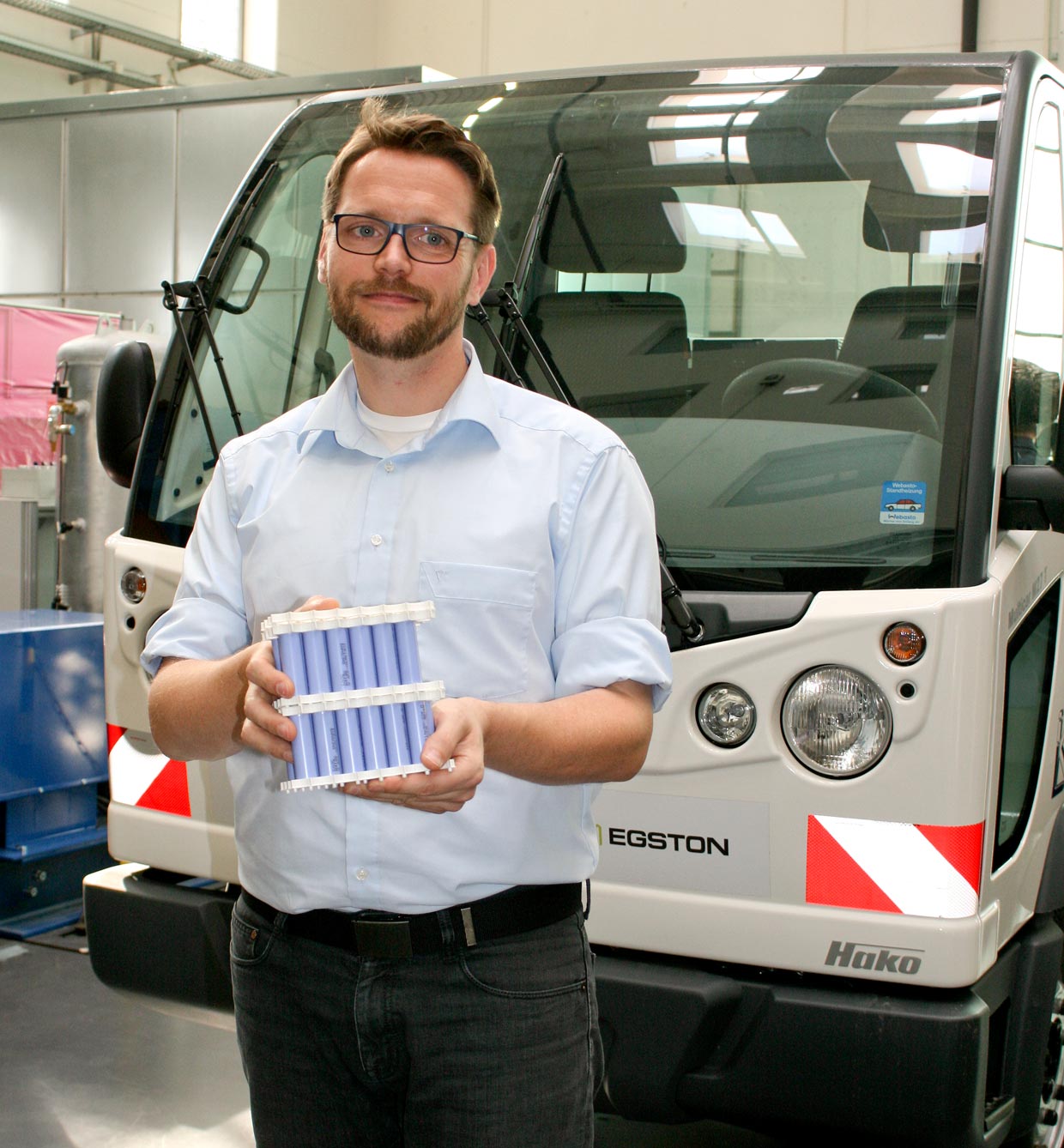
Mit dem Start-up SCABA nutzt das Team um Mitgründer und Gesellschafter Marco Zichner die Möglichkeiten des Leichtbaus für neuartige skalierbare Lithium-Ionen-Batteriesysteme. (Foto: Ina Reichel)
Die Nase vorn mit Carbonfaser-Wicklung
Ebenfalls aus dem ILK hervorgegangen, aber bereits seit 2000 am Markt ist die East-4D Carbon Technology GmbH Dresden. Das heute 60 Mitarbeiter zählende Unternehmen konnte bereits vielfach internationale Kunden aus der Luftfahrt- und Automobilindustrie von seinen CFK-Hightech-Produkten überzeugen. Mit dem patentierten „Filament Winding Forming“ wickelt East-4D beispielsweise nicht nur die „Nasenspitze“ für den Airbus A350-900 XWB, sondern hat mit dem automatisierten Wickelverfahren, bei dem Fasern mit mehrachsig bewegbarer Führung um einen Rohling gelegt werden, auch die Nase vorn im Wettbewerb. Die Technologie ermöglicht in Kombination mit einem speziellen Harz-Injections-Verfahren einen effizienten Materialeinsatz und ist schneller als andere Verfahren, bei denen der Triebwerkseinlaufkegel entweder aus Metall gezogen wird oder die Faserverbunde manuell gelegt werden. Bewährt hat sich diese Methode zur wirtschaftlichen Herstellung von ultraleichten Bauteilen auch für Formel 1-Komponenten und sogar für Ski.
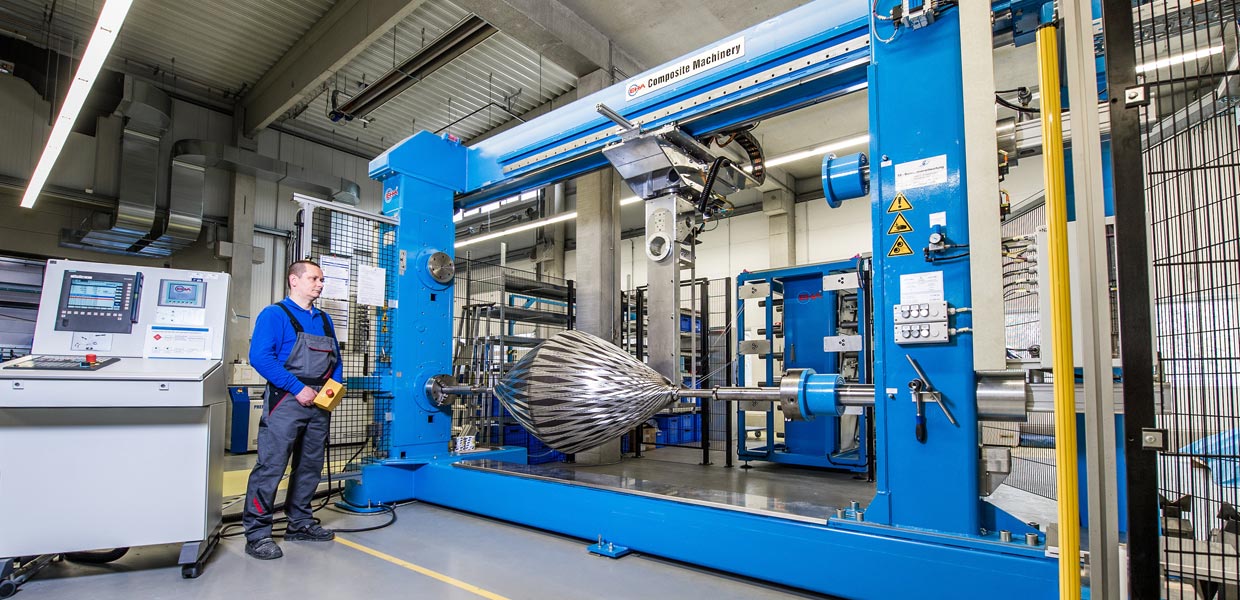
Mit dem patentierten „Filament Winding Forming“ wickelt East-4D beispielsweise Triebwerkseinlaufkegel für Flugzeuge. Auch die Autoindustrie nutzt die Kompetenz des Dresdner Unternehmens für CFK-Hightech-Produkte. (Foto: East-4D)
Neue Materialien in neuen Produkten sichtbar machen
Für zukunftsträchtige Entwicklungen vom Werkstoff bis zur Anwendung sorgen in Dresden rund 2500 Materialwissenschaftler und Techniker in mehr als 20 universitären und außeruniversitären Forschungseinrichtungen. Ihre Kompetenzen bündeln sie im 1993 gegründeten Materialforschungsverbund Dresden (MFD). Auf dieser Basis wird das Know-how national und international gezeigt, beispielsweise auf der BMBF-Plattform FOREL. Hier geht es um Leichtbaulösungen im Multi-Material-Design für die Mobilität der Zukunft. „Die Eigenschaften neuer Materialien werden am besten sichtbar in neuen Produkten. Deshalb haben wir im BMBF-Innovationsforum PRIME die Materialforschung mit dem Mittelstand und der Kreativwirtschaft in Dresden zusammengebracht, um gemeinsam innovative Produktideen zu generieren“, zeigt Prof. Brigitte Voit, Vorstandsvorsitzende des MFD und Wissenschaftliche Direktorin des Leibniz-Instituts für Polymerforschung Dresden, eine neue Form der Interdisziplinarität auf.
Man darf gespannt sein auf die Resultate aus diesem und vielen weiteren Vorhaben der Materialexperten, über die sicher dann zur 3. Werkstoffwoche zu berichten sein wird – vom 18. bis 20. September 2019 wieder in Dresden.