In Zwickau läuft der Umbau des VW-Werkes zu einem reinen E-Mobilitätsstandort auf vollen Touren. Ende November 2019 sollen die ersten ID.3 aus dem Werk rollen. Befeuert wird dieses Ziel vom Pre-Booking für die limitierte Erstedition von 30.000 Fahrzeugen. Innerhalb einer Woche hatten sich ab Starttermin 8. Mai mehr als 15.000 Kaufinteressenten registriert.
Den bestehenden Standort umzurüsten für ein neues Mobilitäts-Zeitalter sei wie „Umziehen im Kleiderschrank“, benutzt Reinhard de Vries, Geschäftsführer Technik und Logistik bei VW Sachsen, ein plastisches Bild für die Herausforderung des Umbaus bei laufender Fertigung. Während auf einer Fertigungslinie noch der Golf mit Verbrennungsmotor vom Band rollt, ist auf der anderen Linie schon vieles umgekrempelt. „Wir sind gut vorbereitet, haben den Umbau sorgfältig geplant“, so de Vries. An eine Alternative denke man gar nicht, der Prozess sei alternativlos und nicht aufzuhalten, sagt er auf eine Frage aus der Journalistenrunde, die Mitte Mai 2019 einen Einblick in den laufenden Umbau bekam.
Automatisierte und digitalisierte Fabrik
Mit der Neuausrichtung der Fabrik werden Automatisierung und Effizienz auf modernste Standards gehoben, wird die gesamte Produktion digitalisiert. Beispiel Karosseriebau: Hier fügen zukünftig 1625 Industrie-4.0-Roboter die Teile für die neuen E-Autos zusammen, setzen dabei in einem ID-Fahrzeug 5800 Schweißpunkte und kleben 138 Meter Nähte. Heiko Rösch, seit 1990 bei VW Zwickau und heute Leiter des Karosseriebaus, verweist auf eine neue 100 Meter lange Seitenteilanlage, die aktuell für die Fertigung verschiedener Modelle programmiert wird. Das ist nur ein kleiner Bereich des geplanten Umbaus. Insgesamt werden im Werk 9000 Tonnen Stahl neu eingebaut und 50.000 Quadratmeter Hallenfläche errichtet. 50 Partnerfirmen sind daran beteiligt. 30 Prozent der bisherigen Anlagen werden wiederverwendet.
Bewegung in der Zulieferlandschaft
Eine Erweiterung erfährt das Presswerk, das wesentliche Teileumfänge für die neuen E-Fahrzeuge inhouse fertigen wird, wie Reinhard de Vries informierte. Volkswagen verspricht sich hiervon reduzierte Logistikkosten und kleinere Regelkreise, um schnellstmöglich die beste Qualität zu erreichen. In den Konzern geholt wird auch die Montage der E-Achsen, die konventionellen Komponenten stellte bisher ein Dienstleister bereit. VW Braunschweig investiert für die Montage in einen neuen Standort im wenige Kilometer von Fahrzeugwerk entfernten Gewerbegebiet Meerane. Dorthin siedeln auch der Cockpit-Zulieferer SAS Autosystemtechnik und der Sitzhersteller Adient um, die bisher in Crossen bzw. Zwickau ansässig waren. Neu als Zulieferer ins Autoland Sachsen kommt der Bordnetzspezialist Leoni. Dafür wird Dräxlmaier seinen Standort in Zwickau schließen. 15 JIS- und 40 Kaufteile-Lieferanten werden die Fahrzeugfertigung direkt beliefern.
Umfangreiches E-Trainingslager
Das neue Produkt E-Fahrzeug sowie der wachsende Grad an Automatisierung und Digitalisierung in der Produktion erfordern auch einen Wandel in den Kompetenzen der Mitarbeiter. Haben an besagter Seitenteilanlage im Karosseriebau bisher neun Mitarbeiter pro Schicht gearbeitet, werden es künftig drei sein. Dennoch wird der Personalbestand von rund 8000 Beschäftigten im Werk konstant bleiben, betont Reinhard de Vries. Zum einen liegt das an der Kapazität, die von derzeit 1350 Fahrzeugen pro Tag auf 1500 steigen soll. Zum anderen wird es große Veränderungen bei den Arbeitsinhalten geben. Es werden weniger Menschen mit der Hand am Produkt arbeiten, dafür müssen viel mehr die Technik betreuen. Das bedeutet: Alle rund 8000 Beschäftigten des VW-Werkes in Zwickau durchlaufen derzeit ein Trainings- und Weiterbildungsprogramm im Trainingscenter für E-Mobilität, um sich fit zu machen für die neuen Aufgaben. Dabei geht es nicht nur um technische Kenntnisse, sondern, wie Dirk Coers, Geschäftsführer Personal erläutert, auch um die mentale Einstellung zur neuen Antriebstechnologie, denn auch in der Mannschaft muss noch Skepsis vor der E-Mobilität abgebaut und das Gefühl für einen völlig neuen Markt geschaffen werden.
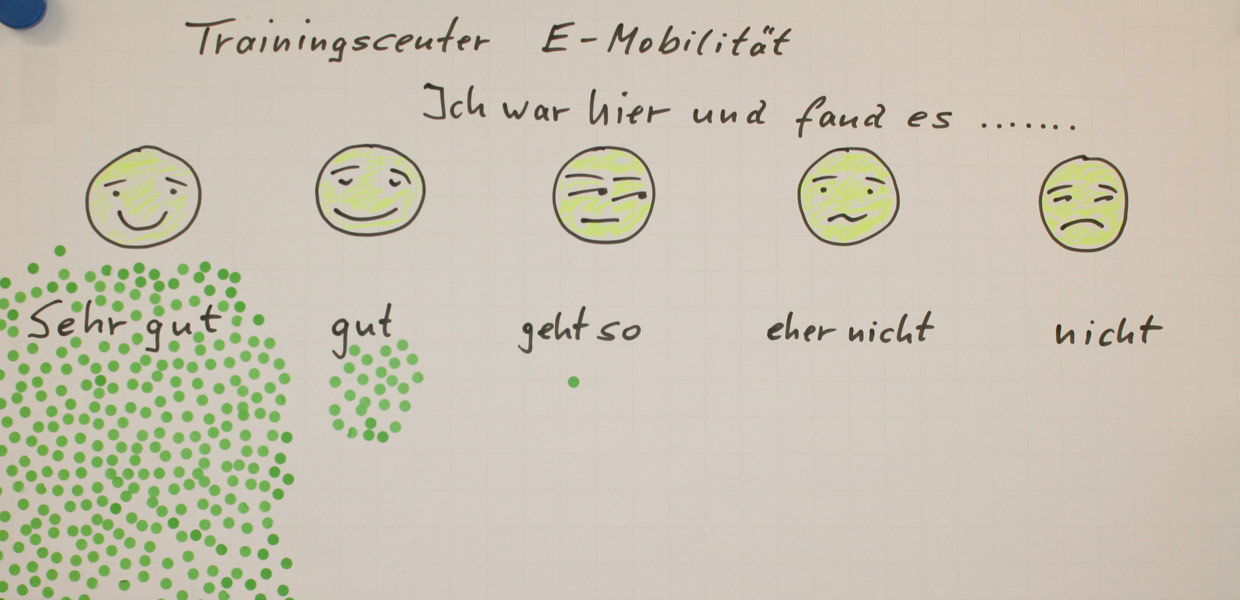
Mit Teamwork den Escape Room meistern
Dafür hat VW Sachsen mit seinem Tochterunternehmen VW Bildungsinstitut und dem Lean Center des Konzerns ein beispielgebendes Konzept entwickelt, das nach dem Escape-Room-Prinzip funktioniert. Teams müssen in einer bestimmten Zeit verschiedene Rätsel knacken und Codes finden, um von einem Zimmer zum anderen zu gelangen. Dabei wird historisches und heutiges Wissen zum Thema Elektrizität vermittelt. Die Aufgabenstellungen wechseln, damit sich kein Team von den Vorgängern die Lösungen schon „beschaffen“ kann.
In weiteren Trainingsräumen werden technische Fähigkeiten und Fertigkeiten trainiert, von den Grundlagen der Elektrotechnik über die Handhabung von neuen Steckverbindungen bis hin zum virtuellen Montagetraining.
Im Escape-Room 1 sind Fragen zur Historie der Elektrifizierung zu lösen, u. a. zum ersten Patent für den Elektromotor, das der Amerikaner Thomas Davenport erhielt. (Foto: Frank Reichel) Die Entwicklung des Zwickauer Automobilbaus von 1904 bis heute im Kontext mit weiteren zeitgeschichtlichen Ereignissen wird in Raum 2 thematisiert. (Foto: Frank Reichel) Die zukünftigen Herausforderungen in punkto Elektromobilität stehen im Mittelpunkt in Raum 3. (Foto: Frank Reichel) Virtuelles Montagetraining. (Foto: Frank Reichel)
Prozesse müssen in der Kette funktionieren
Die Qualifizierungsleistungen für neue Technologien wie Hochvolt-Technik, E-Antrieb, Mensch-Roboter-Kollaboration oder neue Fügeverfahren sowie für IT- und Digitalisierungsprozesse in Produktion, Instandhaltung und Inbetriebnahme bietet VW über das VW Bildungsinstitut ausdrücklich auch den Zulieferern an. „Die Prozesse müssen in der Kette funktionieren“, verweist Dirk Coers auf einen wesentlichen Fakt für das Gelingen der Transformation E-Mobilität.