Der Weg zu einem Prototyp ist bei der Entwicklung von E-Maschinen mit konventionellen Verfahren ziemlich lang. Die Gründer des am 1. Juli 2020 in den Markt gestarteten Unternehmens Additive Drives aus Halsbrücke bei Freiberg verkürzen diesen Zeitraum von Monaten auf Wochen.
Möglich wird das dank additiver Fertigung der Kupferspulen, den Hauptkomponenten im E-Motor. Auf Basis der Konstruktionsdaten erfolgt direkt der 3D-Druckprozess. Additive Drives hat dafür das selektive Kupfer-Laserschmelzen material- und verfahrensseitig optimiert. Das zeit- und kostenaufwendige Herstellen und Einrichten von Werkzeugen, wie es bei herkömmlicher Verfahrensweise notwendig wird, entfällt.
Darüber hinaus gibt es weitere gewichtige Effekte. „Weil 3D-Druck deutlich weniger Restriktionen unterliegt als konventionelle Verfahren, können die Spulen in ihrer Geometrie optimal ausgelegt und angepasst werden. Das spart Bauraum ein, verringert Leitungsverluste und steigert die Effizienz. Bis zu 45 Prozent mehr Leistung haben wir bereits nachgewiesen“, berichten Geschäftsführer Dr. Jakob Jung und der Kaufmännische Geschäftsführer Philipp Arnold. Die beiden jungen Männer besitzen bereits Entwicklungs- und Produktmanagement-Erfahrungen aus ihrer Tätigkeit bei einem Automotive-Engineeringunternehmen. Sie haben Additive Drives gemeinsam mit Lasse Berling und Axel Helm gegründet, den Kompetenzträgern für additive Fertigung und Industrialisierung von Prozessen im Team.
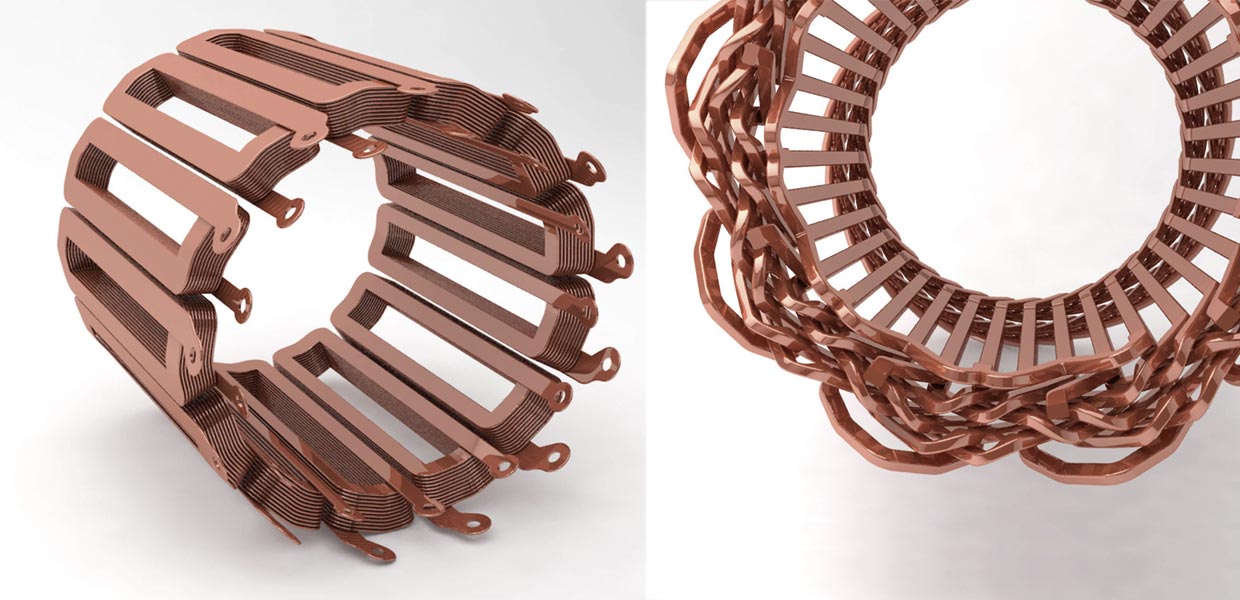
Additive Drives setzt bei Anwendungen in E-Traktionsmotoren auf die sogenannte Hairpin-Wicklung. Dabei ersetzen rechteckige Kupferstäbe gewickelte Kupferdrähte, die mittels 3D-Druck deutlich schneller gefertigt werden können und Versuchsmuster bereits innerhalb weniger Wochen statt mehrerer Monate zur Verfügung stehen. „Das Design und die Materialeigenschaften stimmen mit der konventionellen Fertigung überein. Damit ist ein aussagekräftiges Prototyping gegeben“, betont Dr. Jung.
Während beim Prototyping der Faktor Zeit Regie führt, weil bestehende Konzepte mittels 3D-Druck schneller Serienreife erlangen, können mit additiven Technologien generell völlig neue Entwicklungskonzepte umgesetzt werden. „Wir haben hier einiges in der Schublade, um die E-Maschine grundlegend zu verbessern“, verweist Dr. Jung auf das Zukunftspotenzial. Bereits umgesetzt sind Anwendungen im Rennsportbereich.
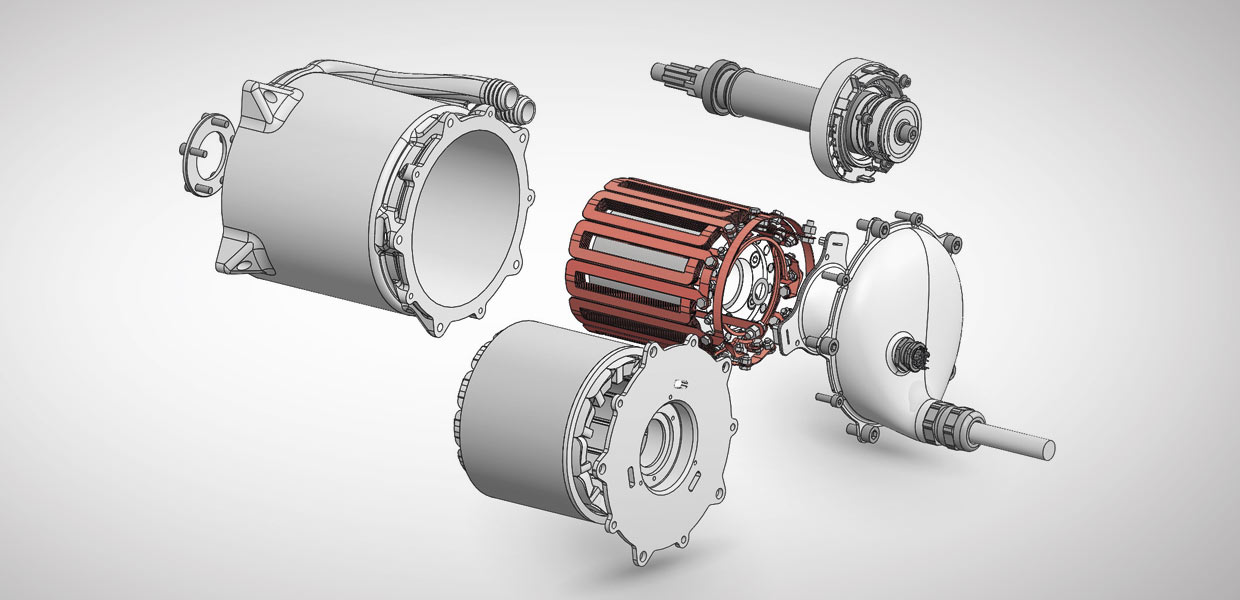
Das junge Unternehmen hat schon viele positive Reaktionen aus dem Markt erfahren. „Wir sind in Gesprächen mit Automobilherstellern und First-Tier-Lieferanten und bahnen erste Projekte an. Unsere DNA ist der Fahrzeugbau. Langfristig können wir uns auch Anwendungen in anderen Branchen vorstellen“, informiert Philipp Arnold.
Neben der weiteren Entwicklungsarbeit am E-Motor und seinen Komponenten ist die Industrialisierung der Fertigung in Richtung wirtschaftlicher Serienproduktion ein Ziel. Dafür hat sich Additive Drives eng mit der internationalen Forschungswelt vernetzt und kooperiert ebenso mit lokalen Technologie- und Fertigungspartnern.
Gefördert wird die Neugründung mit einem EXIST Forschungstransfer an der Professur für Additive Fertigung von Prof. Dr. Henning Zeidler der TU Bergakademie Freiberg. „Durch diese zusätzlichen Mittel können die Gründer ihre Produkte zügig zur Marktreife entwickeln und das potenzialreiche Unternehmen in einem stark wachsenden Markt etablieren“, erklärt Andre Uhlmann vom Gründernetzwerk SAXEED an der TU Bergakademie Freiberg, das das Team von Additive Drives unterstützt.