Die DGH-Group gehört zu den führenden europäischen Anbietern von Druck- und Sandgussteilen. Die Aluminium- und Magnesium-Komponenten des Unternehmens mit Sitz im sächsischen Dohna sowie weiteren Werken in Hof und Friedrichshafen sind in den Antriebssträngen zahlreicher Fahrzeugmodelle zu finden.
Angesichts des Wandels in der Automobilindustrie steht für Christoph Müller, Vorsitzender der Geschäftsführung der DGH-Group, nicht ein Duell konventioneller versus elektrischer Antrieb auf der Tagesordnung. Vielmehr zählen Lösungen für eine den jeweiligen Bedingungen angepasste ökonomisch wie ökologisch sinnvolle Mobilität. Ideen sind deshalb in allen Bereichen gefragt. „Bei einem prognostizierten Anteil von 20 bis 25 Prozent E-Mobilität 2025 bleibt immer noch ein Übergewicht von 75 bis 80 Prozent für den Verbrennungsmotor“, so der DGH-Chef.
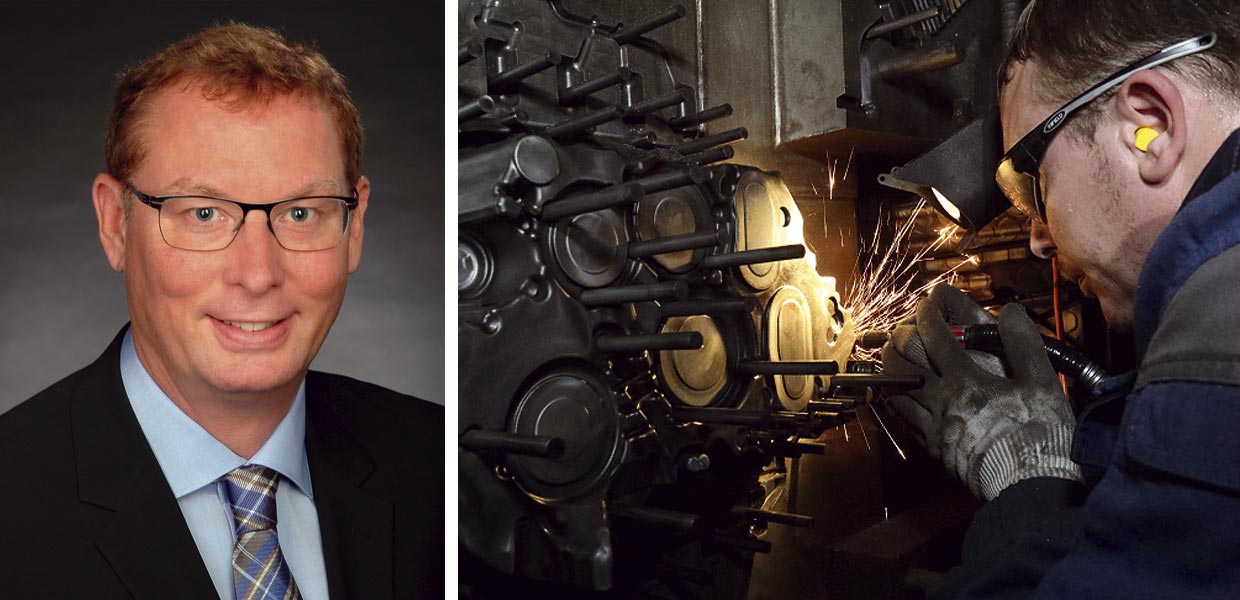
Wärmebehandlung wird integriert
In der Gruppe wird die Zeit genutzt, um in neue Technologien hineinzuwachsen, das Produktportfolio zu erweitern sowie in andere Branchen wie Heizungs- oder auch Medizintechnik zu diversifizieren. Das Unternehmen integriert den Bereich Wärmebehandlung in seine Wertschöpfungskette, die bereits die gießtechnische Teileentwicklung, die Werkzeugkonstruktion, den Gießprozess, die mechanische Bearbeitung und die Montage umfasst. „Damit sind wir in der Lage, neben Komponenten für den Antriebsstrang auch Strukturteile für die Karosserie anzubieten. Wir kooperieren hier mit einem Partner und können beide unser Geschäft ausbauen“, verweist Christoph Müller auf Synergien.
Einstieg in E-Mobilität
Effekte bringt auch die Einbindung einer Sandgießerei in Friedrichshafen in die Gruppe. „Mit diesem Standort sind wir in die Elektromobilität eingestiegen, denn im Sandguss lassen sich geometrisch komplexe Teile in kleinen bis mittleren Serien günstig fertigen. Mit dem Hochlauf der E-Mobilität verfügen wir dann über die Voraussetzungen, die Produktion in den auf Großserie ausgelegten Druckguss zu überführen“, erläutert der DGH-Chef. Das Unternehmen arbeitet u. a. an Auslegung und Fertigung von Gehäusen für Elektromotoren, an Batteriekästen sowie Hybrid-Getrieben. Im Foyer am Hauptsitz in Dohna belegt der Prototyp eines 48-Volt-Getriebes die Kompetenz von DGH für die Entwicklung und Herstellung komplexer Systeme in der Verbindung konventioneller und neuer Verfahren. So ist das Generatorgehäuse additiv gefertigt.
Neben dem Pkw-Bereich verstärkt das Unternehmen seine Aktivitäten für Nutzfahrzeuge. Auch hier ist Innovation der Schlüssel zum Erfolg. Mit Forschungs- und Industriepartnern hat DGH ein Verfahren entwickelt, das im Niederdruckguss arbeitet. „Damit können wir kleinere Maschinen nutzen, sparen Werkzeug- und Fertigungskosten. Hinzu kommt, dass wir mit dieser Technologie ein ursprünglich zweiteiliges Getriebe jetzt einteilig auslegen und herstellen können. Wir haben in diesem Projekt eng mit dem Kunden zusammengearbeitet, auf Augenhöhe“, betont Christoph Müller.
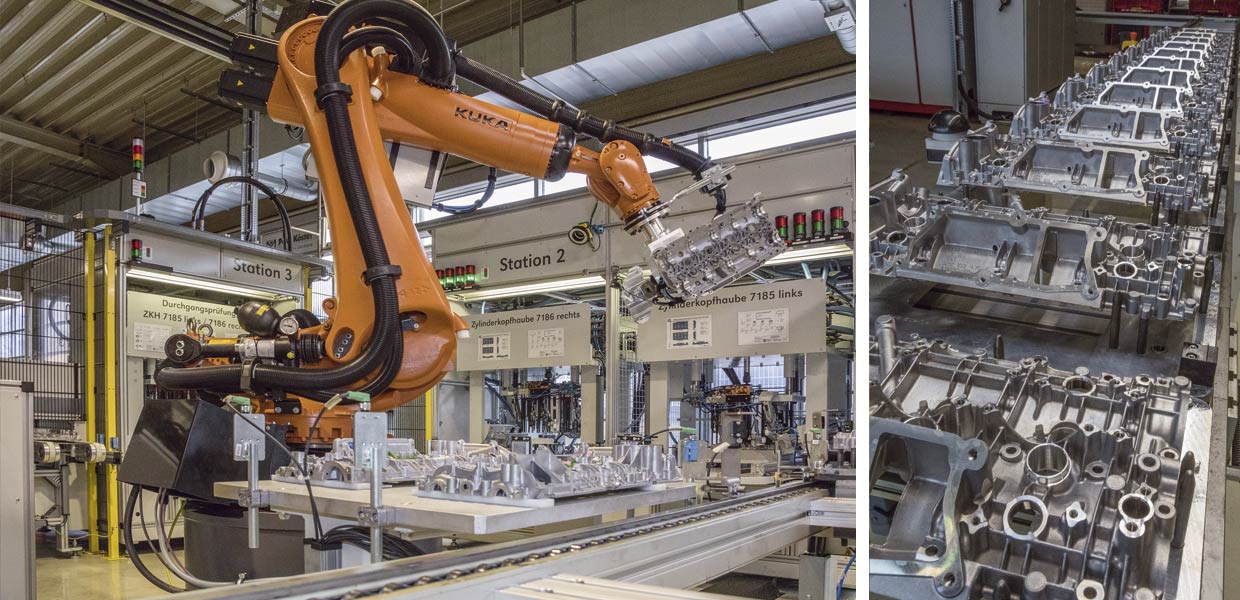
Unsichere Lage belastet Verhältnis zwischen Hersteller und Zulieferer
Das ist leider nicht immer der Fall. Hersteller geben den Druck, der aus der allgemein unsicheren wirtschaftlichen Lage resultiert, an Zulieferer weiter und verschärfen Spannungen. Hinzu kommt für Christoph Müller ein enttäuschendes Verhalten der Politik, die tatenlos zusieht, wie eine deutsche Vorzeigebranche niedergemacht wird. Die DGH-Group mit rund 1000 Mitarbeitern steuert mit ihrer strategischen Ausrichtung und im engen Austausch mit Betriebsrat und Gewerkschaften gegen. „Die Innovativen werden überleben“, so die Überzeugung von Christoph Müller.