Mit einem in der Gläsernen Manufaktur Dresden angesiedelten Inkubator-Programm unterstützt Volkswagen kreative Start-ups, die frische Ideen für Mobilitätsdienstleistungen der Zukunft oder Innovationen im Bereich Produktion und Logistik 4.0 haben. Seit dem Start im August 2017 dominierten Themen der Digitalisierung rund um Fahrzeug, Infrastruktur und Fertigung. In Klasse 4 des Inkubators zog im Mai 2019 ein junges Unternehmen ein, dass mit einer anderen Ausrichtung unterwegs ist – auf einem erfolgversprechenden Holz-Weg.
Seit Januar 2018 gibt es die vierköpfige LiGenium GmbH Chemnitz. Geschäftsführer Christoph Alt hat das Unternehmen mit weiteren Mitstreitern aus der Professur Fördertechnik der TU Chemnitz ausgegründet. Ihr Ziel: den nachwachsenden Werkstoff Holz für effiziente und nachhaltige Anwendungen im Maschinenbau zu nutzen. Ihre Kompetenz: die Verbindung von maschinenbautechnischem Wissen und Know-how für die Nutzung des Konstruktionswerkstoffs Holz. „Mit dieser Kombination besetzen wir eine Nische und bauen darauf ein ganz neues Produktportfolio auf“, verweist Christoph Alt auf die LiGenium-Expertise, die dem Unternehmen eine herausragende Stellung am Markt bringt.
Belastbare Leichtgewichte
Die ehemaligen TU-Mitarbeiter setzen auf bereits erfolgreich realisierte Projekte aus der Universitätszeit auf. Dazu gehört eine Skidförderstrecke für den innerbetrieblichen Karossentransport im VW-Werk Wolfsburg. Neben Transportrollenbahnen mit Gestellsystemen in moderner Holzbauweise umfasst die LiGenium-Produktpalette u. a. Transportwagen für die Intralogistik sowie Sonderladungsträger für den überbetrieblichen Teiletransport. „Solche Ladungsträger bestehen heute meist aus Stahl. Ihr Eigengewicht ist teilweise bis zu zehn Mal höher als das zu transportierende Gut. Diese zu bewegende Masse treibt auch die Transportkosten und den Treibstoffverbrauch in die Höhe. Holz bietet hier eine wirtschaftliche und ökologische Alternative für anspruchsvolle langlebige technische Anlagen und Bauteile“, betont Christoph Alt und verweist auf die Vorteile dieses über Jahrzehnte „vergessenen“ Konstruktionswerkstoffs. Beispielsweise können Ladungsträger und weitere Maschinenbauelemente bis zu 50 Prozent leichter hergestellt werden als konventionelle Konstruktionen und das bei mindestens gleicher Belastbarkeit. Das LiGenium-Team arbeitet u. a. an einem für fahrerlose Transportsysteme tauglichen Holz-Standardmodul mit 15 Kilogramm Eigengewicht, das bis zu einer Tonne Material befördern kann.
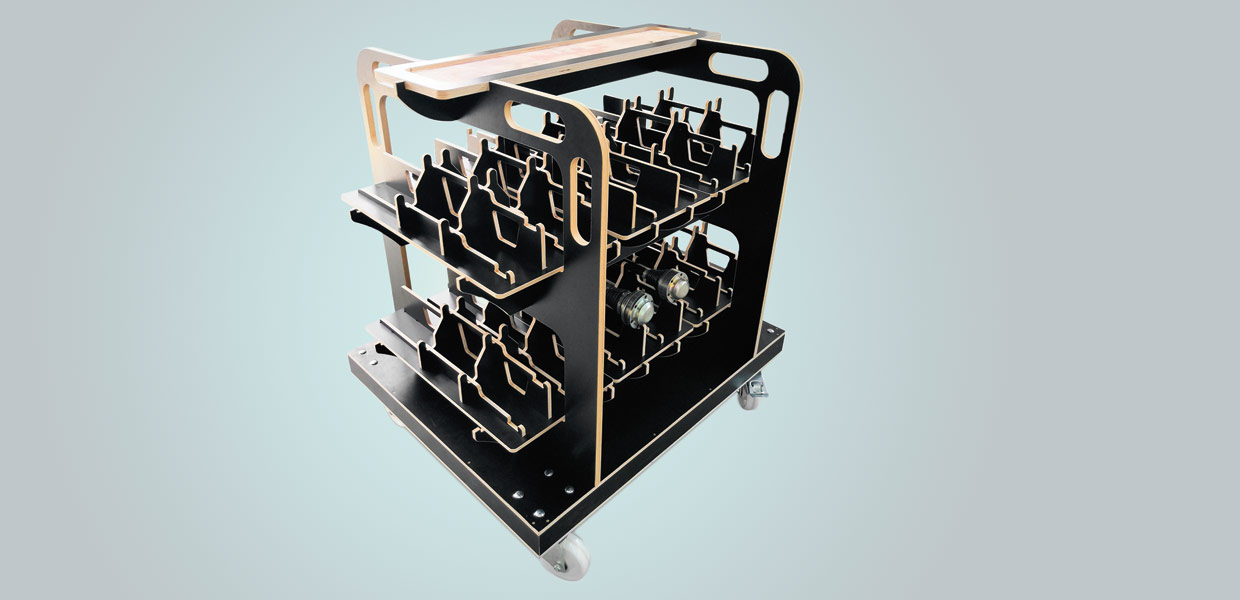
Holz schlägt Stahl bei CO2
Schwingungsdämpfung, Lärmreduktion und elektromagnetische Verträglichkeit (EMV) sind ebenfalls Eigenschaften pro Holz. „Gerade das Thema EMV eröffnet Möglichkeiten, in Transportwagen oder Ladungsträger WLAN- und Funksignaltechnik sowie weitere Funktionen zu integrieren, Prozesse in Echtzeit zu überwachen und jederzeit Aussagen zum Zustand der Fördertechnik zu erhalten“, erläutert Christoph Alt.
Ein weiteres Plus von „Holz im Maschinenbau“ rückt mit den sich verschärfenden Klima-Zielen immer mehr in den Vordergrund: Pro Tonne Rohstahlerzeugung werden nach Angaben der Wirtschaftsvereinigung Stahl 1,34 Tonnen CO2 emittiert. Holzprodukte sind dagegen Kohlenstoffspeicher. Je mehr andere CO2-verursachenden Materialien durch Holzprodukte ersetzt werden, desto mehr CO2-Emissionen können verhindert werden. Experten gehen davon aus, dass eine Tonne Holz, die als Ersatz für andere Werkstoffe dient, die CO2-Emissionen um durchschnittlich zwei Tonnen reduziert.
Mit diesem ökologischen „Fußabdruck“ wird der Einsatz von Holzkonstruktionen in der Automobillogistik immer interessanter. Auf dem jüngsten Innovative Logistics Solution Day der VW-Konzernlogistik im Mai 2019 war das LiGenium-Team mit dem dort gezeigten Pilotprojekt für Logistikprozesse in der Produktion eines Elektro-Sportwagens ein gefragter Gesprächspartner aller Konzernmarken.
Während der halbjährigen Inkubator-Phase in der Gläsernen Manufaktur treibt das Chemnitzer Start-up ein weiteres Projekt voran die Substitution eines palettenförmigen Stahl- durch einen Mehrweg-Holzladungsträger, mit dem zukünftig in der Manufaktur Sitze vom Lkw über einen Aufzug zum Verbauort befördert werden. Darüber hinaus wird an der Idee für einen neuen Kommissionierwagen sowie an weiteren Projekten für die Automobilindustrie gearbeitet. „Wir wollen in dieser Zeit so viel wie möglich Anregungen erfahren und Anwendungen erproben, um auf dieser Basis perspektivisch ein Portfolio an Grundmodulen zu entwickeln, die sowohl für Großunternehmen als auch für den Mittelstand nutzbar sind“, so Christoph Alt.