Ein neues Konzept zur effizienten Fertigung crashbelasteter Leichtbauteile präsentieren Forscher der TU Chemnitz und des Fraunhofer-Instituts für Werkzeugmaschinen und Umformtechnik IWU Chemnitz auf der „K 2019“.
Wissenschaftler der drei Professuren Festkörpermechanik, Werkstoff- und Oberflächentechnik sowie Werkstoffwissenschaft der Technischen Universität Chemnitz und des Fraunhofer IWU Chemnitz haben einen sogenannten intrinsischen Hybridverbund für crashbelastete Strukturbauteile konzipiert und in einem seriennahen Fertigungsprozess hergestellt. Ein intrinsischer Hybrid ist ein integrales Bauteil, bei dem die Verbindung verschiedener Materialien bereits im Ur- bzw. Umformprozess erfolgt, so dass kein nachgeschalteter Fügeprozess notwendig ist. Ein Demonstrator-Bauteil sowie weitere im Rahmen des von der Deutschen Forschungsgemeinschaft (DFG) geförderten Schwerpunktprogrammes 1712 erzielten Ergebnisse stellen die Forscher vom 16. bis 23. Oktober auf der Fachmesse „K 2019“ (Halle 7, Stand SC10) in Düsseldorf vor.
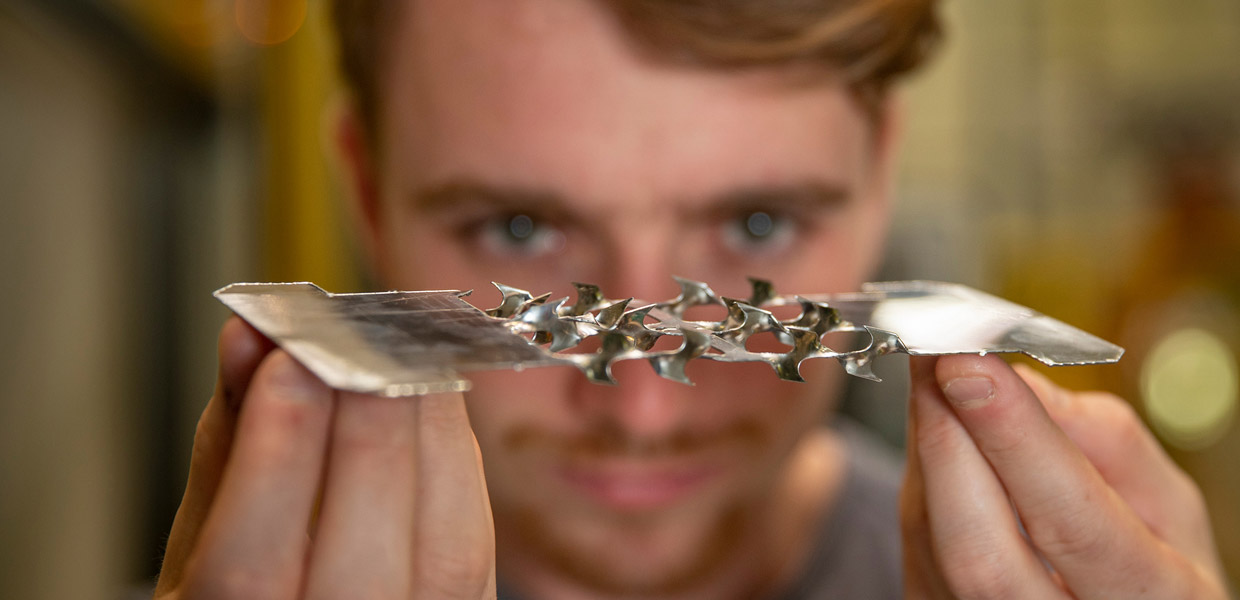
Typischerweise haben Faserverbundwerkstoffe im Crashfall das Defizit einer unzureichenden Energiedissipation, das Verformungsverhalten ist also ungünstig. Diesem wurde im neu entwickelten Konzept entgegengewirkt, indem eine gezielte Verstärkung des eingesetzten faserverstärkten Kunststoffes durch einen metallischen Einleger erfolgt. Mit dem Ziel einer ressourceneffizienten Fertigung wurden bislang sequenziell ablaufende Prozessschritte in einem Schritt zusammengefasst. Im Vorfeld der Fertigung wird der speziell entwickelte metallische Einleger als noch ebene Struktur zwischen die Lagen aus faserverstärktem Kunststoff eingebracht. Während der Erzeugung der makroskopischen Bauteilgeometrie richten sich durch die Wirkung einer Zugkraft Formschlusselemente aus dem Einleger auf und verhaken sich mit dem faserverstärkten Kunststoff. Dadurch kommt es zur Ausbildung eines Formschlusses, der die Kraftübertragung zwischen den Komponenten erheblich verbessert. Zusätzlich wird der metallische Einleger in einem großserientauglichen Sol-Gel-Verfahren beschichtet. Dies verhindert zuverlässig Kontaktkorrosion und verbessert zugleich die adhäsive Anbindung zwischen dem Metall und dem faserverstärkten Kunststoff.
Unterstützt durch Finite-Elemente-Simulationen unter Verwendung neuartiger Materialmodelle wurde dieses Konzept optimiert und bereits im Rahmen der Fertigung des Demonstrator-Bauteils, das auf der „K 2019“ ausgestellt wird, erprobt. Eine umfassende mechanische Prüfung dieses Bauteils bestätigte eine sehr gute Crashperformance bei einem geringen Bauteilgewicht.
Hintergrund: Im Rahmen des von der DFG geförderten Schwerpunktprogrammes 1712 werden Konzepte zur ressourceneffizienten Fertigung, Charakterisierung und Auslegung von intrinsischen Hybridbauteilen entwickelt. Über eine Förderperiode von sechs Jahren werden Bauteile aus metallischen und endlosfaserverstärkten Materialien konzeptioniert, bei denen die Verbindung der unterschiedlichen Materialien im Ur- beziehungsweise Umformprozess erfolgt. Ein bisher üblicher nachgeschalter Fügeprozess ist somit nicht mehr erforderlich.