Die additive Fertigung verlässt zunehmend das Prototypenstadium und bahnt sich den Weg in die Serienproduktion. Zur Umsetzung der auch 3D-Druck genannten Schlüsseltechnologie bei Automobilherstellern und Zulieferern diskutierten am 17. April 2018 in Leipzig die Teilnehmer der Drive-Connection, einer Veranstaltung der Wirtschaftsförderung Leipzig mit dem sächsischen Automobilzuliefernetzwerk AMZ und dem mitteldeutschen Rapid-Prototyping-Netzwerk enficos.
Die OEM sind dabei, sich die Potenziale des Additive Manufacturings (AM) inhouse zu erschließen. BMW richtet seine AM-Strategie auf die Ersatzteilversorgung, die Produktindividualisierung, den Rennsport sowie auf die funktionale und geometrische Absicherung im Entwicklungsprozess aus, wie Thomas Augustin und Patrick Schroth aus dem BMW-Werk Leipzig berichteten. Gerade in der Vorserienentwicklung reichen virtuelle Daten allein nicht aus, um z. B. Ergonomie oder Verbaubarkeit zu überprüfen. Mit 3D-Druck statt aufwändigem Werkzeugbau sind sehr kurze Iterationsschleifen möglich. BMW setzt darüber hinaus 3D-Druck für die Serienfertigung ein, so bei dem in Leipzig produzierten neuen i8 Roadster. Für das Fahrzeug wurde eine AM-Metallkomponente entwickelt und in die Serie überführt. Es handelt sich um die Halterung der Verdeckabdeckung. Ihre Herstellung wäre im traditionellen Gießverfahren in der jetzigen Form nicht möglich gewesen. Das Teil hat eine deutlich höhere Steifigkeit, spart über 40 Prozent an Gewicht und 30 Prozent an Kosten ein.
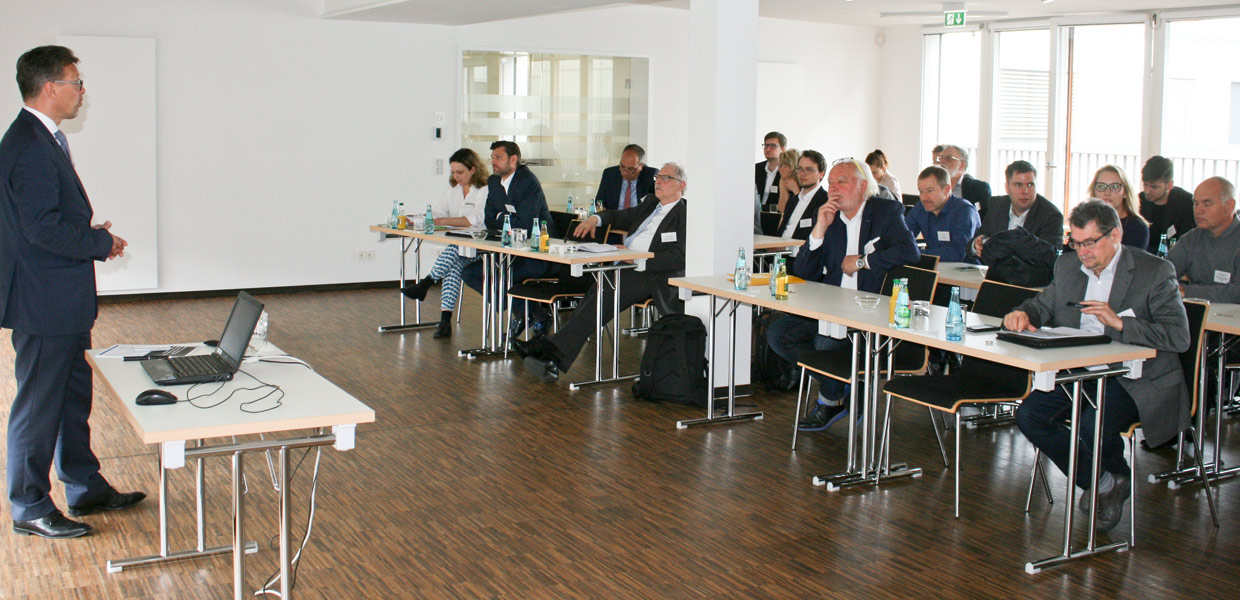
Matthias Heinrich von der Georg Fischer GmbH erläuterte die Beweggründe, als Gießerei in den 3D-Druck zu investieren. (Foto: Ina Reichel)
Viel Aufwand hat BMW in die Wahl des passenden Materials sowie in eine prozesssichere, reproduzierbare Fertigung investiert. Die für dieses junge Technologiefeld generell noch fehlenden Richtlinien und Normen sind auch ein Grund, weshalb Zulieferer bisher kaum 3D-gedruckte Teile anbieten. Zu lernen, wie Konstruktion und Fertigung neu zu denken sind, wie die Prozesse funktionieren sowie sich über Netzwerke das nötige Know-how zu verschaffen und bereit zu sein für die Anforderungen der OEM, dazu ermunterten enficos-Vertreterin Petra Wallasch und AMZ-Netzwerkmanager Andreas Wächtler die Anwesenden.
Die damit verbundenen Chancen zeigte Matthias Heinrich, Geschäftsführer der Georg Fischer GmbH, auf. Er erläuterte die aus additiver Fertigung resultierenden Wettbewerbsvorteile bei der Gussteilentwicklung. Am Standort Leipzig, an dem u. a. Gusskomponenten für Nutzfahrzeuge, Baumaschinen, Land- und Forsttechnik hergestellt werden, hat der schweizerische Konzern in eine 3D-Kerndruckerei investiert. Dank additiv gefertigter Kerne kann der externe Modellbau entfallen. Das führt bei der Herstellung von Teilen für Prototypenfahrzeuge und bei Kleinserien zu enormer Zeit- und Kostenersparnis und gestattet völlig neue gestalterische Freiheiten.
Mittels 3D-Druck können bisher nicht herstellbare Geometrien erzeugt werden, mit denen Produkte gewichts- und leistungsoptimierter werden. Das Leichtbaupotenzial dieser der Natur abgeschauten bzw. nachgeahmten bionischen Strukturen stellte Dietmar Glatz von der Hochschule Merseburg vor.